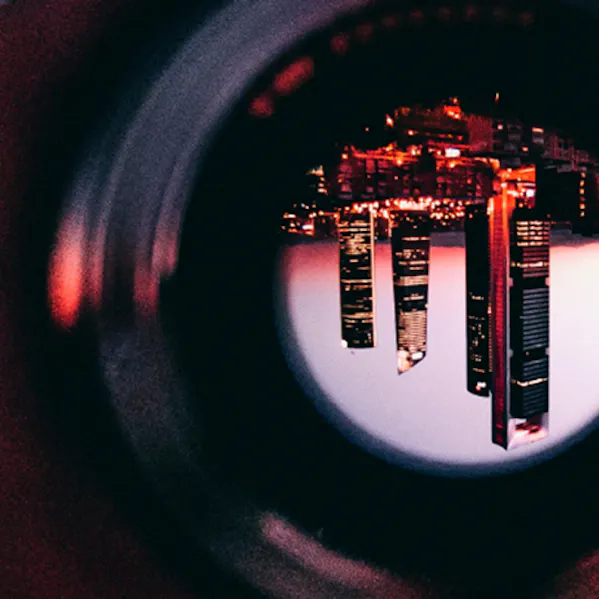
WMU Weser Metall Umformtechnik GmbH
-
Branche
Automotive, Metallverarbeitende Industrie -
Thema
Intelligentes ERP
WMU Weser Metall Umformtechnik GmbH - Das Unternehmen
Die WMU ist ein führendes Unternehmen in der Herstellung und Just-In-Time-Lieferung von Press-, Zieh- und Stanzteilen für die Automobilindustrie. Seit 1999 gehört die WMU zur EDAG Engineering + Design AG, dem weltweit führenden Komplettentwickler der Automobilindustrie mit Hauptsitz in Fulda und 26 weiteren Standorten.
Intelligentes ERP
Das SAP-Projekt
WMU suchte nach einer Lösung mit Funktionen für alle Unternehmensbereiche und entschied sich für eine Branchenlösung auf Basis von SAP ERP. "Wir wollten mehr Transparenz und Planungssicherheit über alle Prozesse hinweg schaffen - vom Einkauf der Rohstoffe bis hin zum Produktverkauf", fasst Mark Pöpperl von Weser-Metall-Umformtechnik, die Projektziele zusammen. "Für All for One Steeb als Partner haben wir uns entschieden, weil sie unsere Situation als Mittelständler versteht und darüber hinaus noch über exzellente Branchenkenntnisse im Automotive-Bereich verfügt", lautet sein Fazit.
Nach vier Monaten startklar
Als die Implementierung im August 2006 begann, war das Unternehmen bestens vorbereitet. Schon im Vorfeld hatte WMU das neue Prozessdesign genau überlegt und die Stammdaten im Altsystem bereinigt. So stand die Software schon nach vier Monaten bereit. Unterstützt wurde WMU dabei von den IT-Fachkräften des EDAG-Konzerns. Zusätzlich standen bei besonders kniffligen Fragen die Experten der All for One Steeb zur Seite. "Das Projekt ist sehr gut gelaufen, weil alle Partner in jeder Phase perfekt kooperiert haben", berichtet Mark Pöpperl.
Profitabilität differenziert auswerten
Mit Hilfe der Branchenlösung hat das Management die gesamte Wertschöpfungskette sicher im Blick. Vor der Umstellung existierten zwei getrennte Systeme, eines für Logistik, ein anderes für Finanzwesen und Controlling. Über die alte Produktionssoftware liefen die mengenmäßigen Transfers bis hin zur Fakturierung an den Kunden. Anschließend erfolgte die Datenübergabe an die Finanz- und Controllingsoftware. Zwar wusste die Finanzabteilung damit, was das Unternehmen eingekauft und verkauft hatte - die Wertzuwächse über die einzelnen Produktionsschritte hinweg ließen sich jedoch nicht ermitteln.
Kauft das Unternehmen dagegen heute Rohstoffe ein, werden diese sofort gebucht und in die Produktion gegeben. Gleichzeitig fließt eine Meldung in den Finanzbereich. Das geschieht auch nach den jeweils nächsten Produktionsschritten. "Wir kennen die Wertschöpfung und unsere Kosten bei jedem Produktionsschritt. Dadurch wissen wir, wie profitabel wir arbeiten und wo noch Verbesserungsbedarf besteht", erklärt Mark Pöpperl die damit verbundenen Vorteile.
Material und Personal exakt disponieren
Unterstützt von der SAP-Anwendung hat das Unternehmen viele der zuvor manuellen Prozessschritte automatisiert. So teilt der Kunde auf elektronischem Wege mit, bis wann er welche Menge benötigt. Diese Vertriebsinformation stößt die weiteren Geschäftsabläufe an: Die Auftragsbearbeitung macht Versandvorschläge, die automatisch in die Produktionsplanung einfließen und Bestellungen für fehlende Rohmaterialien auslösen.
Zugleich gibt der Vertrieb Planwerte ein, bis wann wie viele Teile von welchem Material fertiggestellt sein müssen. So lassen sich Material und Personal langfristig disponieren. "Früher mussten wir langwierig mittels Tabellenkalkulation planen. Das geht heute automatisch, und wir haben sehr viel mehr Möglichkeiten", erläutert Mark Pöpperl. Beispielsweise lassen sich mit Hilfe der integrierten Abrufsteuerung Versand, Produktion und Rohstoffbeschaffung exakt terminieren. Da die Software die jeweiligen Beschaffungs- und Produktionszeiten kennt, erfolgt automatisch eine Bestellung der erforderlichen Materialien, sobald eine kritische Mindestmenge unterschritten ist. "Dadurch können wir genau disponieren und die Lagerhaltung entsprechend straff halten.
Vorher hatten wir bei einem hohen manuellen Aufwand für die Dispositionskontrolle mitunter immer noch Lieferengpässe", räumt Pöpperl ein.
Mehr Effizienz - exaktere Planung
Die neue Infrastruktur hat sich bereits nach kurzer Zeit bezahlt gemacht. Dies zeigt sich eindrucksvoll an einem einfachen, aber sehr plakativen Beispiel: Im April führten Mitarbeiter die erste Vollinventur durch. Früher benötigten sieben Mitarbeiter dafür zwei Tage, und die Abweichungen lagen auch schon mal zwischen 100.000 und 150.000 Euro. Heute erledigt dasselbe Team die Aufgabe an einem Tag bei einer Inventurabweichung von knapp 15.000 Euro.
Kundennutzen
- Abbilden aller Kernprozesse in einem integrierten System
- Industriestandard
- Zukunftssicherheit
Projektzusammenfassung